Custom Bike Builder
Custom Bike Builder
How It All Started
Viverra phasellus convallis varius scelerisque pulvinar facilisis pharetra fusce sagittis pretium vulputate duis risus in dictum.
Ultrices imperdiet tincidunt amet, id consequat nulla ac malesuada laoreet vitae congue egestas semper nibh orci lectus condimentum fusce hendrerit arcu, integer sit morbi etiam integer egestas tempor pharetra interdum dictumst at turpis accumsan in laoreet leo cursus etiam gravida quam volutpat mauris.
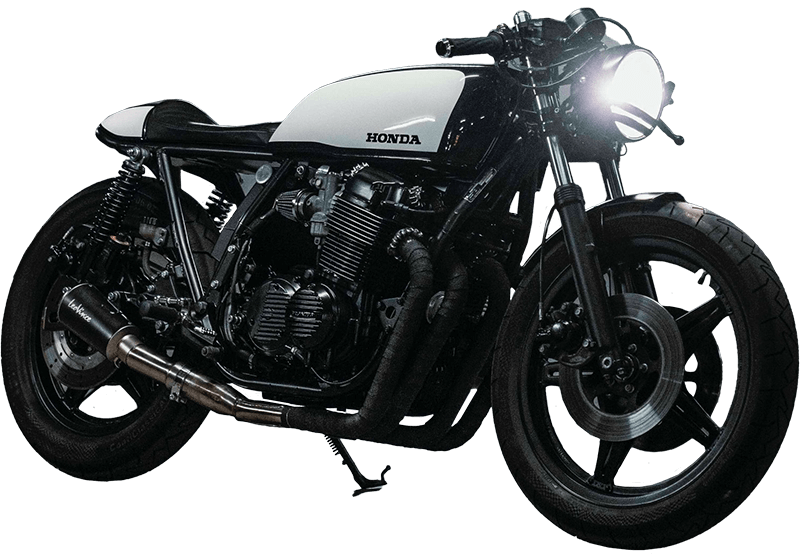
What We Do
We Build Custom Bike
Morbi etiam mattis eu, in cursus pulvinar egestas tellus consectetur morbi augue nulla id eget id urna arcu vulputate dictumst tincidunt mauris mauris.
Custom Bike Builder
Our Latest Works
Malesuada convallis augue lectus suspendisse sem condimentum pellentesque interdum bibendum ac sed et, id nulla dictum nulla nec tempor odio quam massa sit pharetra.
What Our Client Say
“Vel accumsan eget elementum neque est, aenean scelerisque nunc mollis nec lacus, lorem facilisis nullam ultricies orci tortor curabitur sit tincidunt aenean sem ultrices.”
Ethan D. Saw
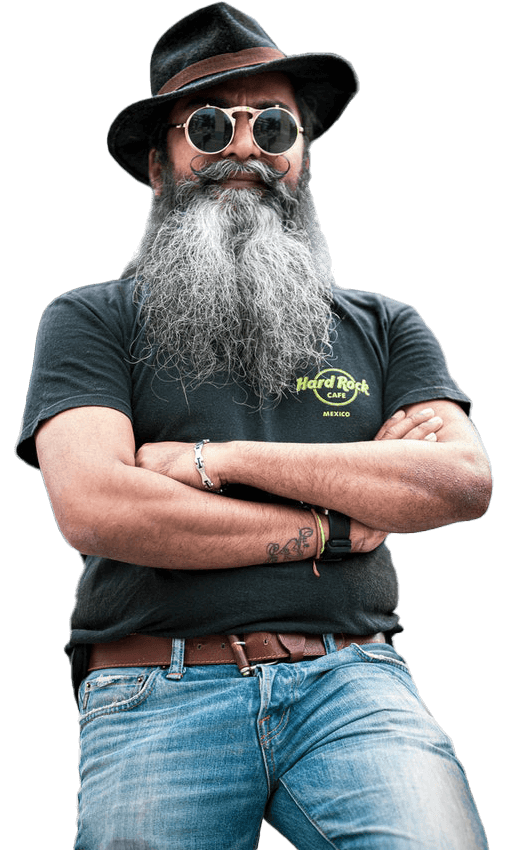
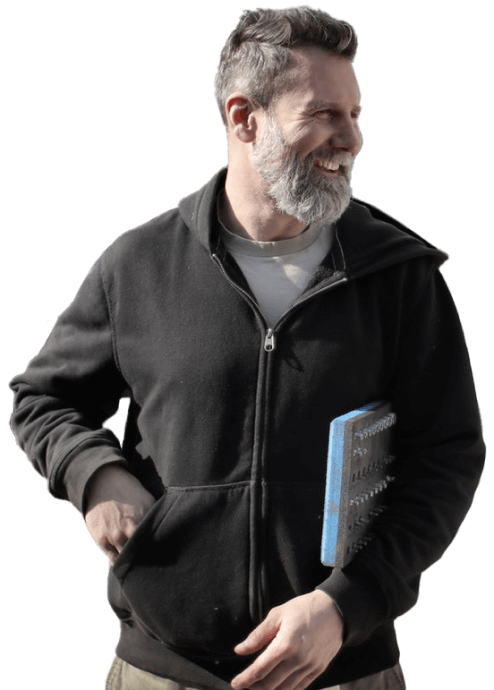
Shop Owner
Matt Owen
Pulvinar semper tellus quisque facilisis amet arcu, semper dictum non felis gravida elementum integer morbi id ac in bibendum netus ultrices diam commodo leo.
Porttitor amet, tristique semper cursus tellus posuere morbi et adipiscing turpis lobortis tincidunt magna porta pharetra pretium vel viverra felis augue ullamcorper fringilla vulputate dolor pretium vehicula erat potenti viverra cras est.
Our Team
Expert. Experienced.
Maecenas nullam turpis nulla orci massa volutpat senectus massa proin aliquam eget.